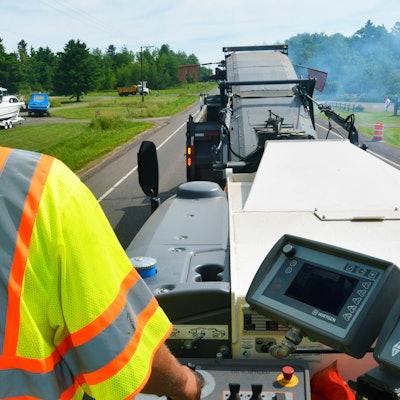
From its base in Lakeville, MN, a Minneapolis suburb, Midstate Reclamation & Trucking is leveraging its fleet of reclaiming, cold milling and in-place recycling equipment to grow its market while serving long-time customers.
Midstate was launched in 1991 and brought in the first reclaimer to Minnesota in spring 1992.
"After being in trucking for a number of years, I figured there had to be a better way to make a living," Tom Johnson, chief executive officer says. "In my research I saw how you could take a piece of asphalt, grind it up and turn it to gravel. We worked with the state to establish a standard specification for that product, and the business took off from there.
"We believe in our mission. We are saving taxpayer money by preserving and building superior pavements for less money, in less time and in an environmentally friendly manner. Our mission is stewardship. We are making tax dollars go farther while greatly cutting down on truck trips, greatly reducing total truck emissions and traffic congestion. And re-use of materials in-place saves virgin aggregates and prolongs the life of quarries and gravel pits, which are encountering permitting challenges of their own."
In the late 1990s Midstate helped develop specs for cold in-place recycling in its home state and now executes that work through the northern tier of states.
"Midstate has been a driving force behind 100% in-place recycle and every couple of years we seek out another discipline to explore," Johnson says. "We started with reclaiming, then got into cold in-place. Then we brought soil stabilization and cold milling into the fold. Now we are looking at cold central plant recycling. We've pioneered every single process that's been out there the last 25 to 30 years.
"Every road theoretically is failing and it has a lot to do with what it's built on," he adds. "Every subgrade likely has poor soils in it. When we were building roads decades ago, they would strip the topsoil and pave on that. Up here, there are many miles of full depth asphalt resting on clay and these roads are failing. It's not what roads are built of, it's what they are built on."
Counties Lead Way
In those days, regardless of technique, Johnson found that local governments were more accepting of preservation, in-place recycling and base reclamation than the state DOTs were. "The counties have been way ahead of the states on this," he says. "We got farther with the counties in a shorter period of time than the states because counties led the charge. And 25 years later, the states are finally getting on board."
That's because at the county level -- so long as federal money has not been involved -- local government has more latitude to initiate these processes. "We have been getting more of a charge from the bottom-up than the top-down," he adds.
To better serve its clients, Midstate shifted to a high-technology equipment platform when it acquired its first piece of Wirtgen Group equipment. "Their technology leads the rest of the industry and they have led the pack in cold mills and reclaimers," Johnson says.
Today, Midstate has over 100 employees and operates in a core of 13 states, including Minnesota, Iowa, Florida, Indiana, Colorado, North Dakota, Nebraska, Illinois, Montana and Wyoming. It works for governments and real estate developers as well a sub for prime contractors.
Midstate’s first Wirtgen cold mill was a W 2200 with an 8-ft., 2-in. drum. "That was a monster," Johnson says. "We were cutting 13 inches of asphalt and just tearing it out. The W 2200 changed the market in cold milling and changed the way we conduct milling."
Midstate now has a variety of Wirtgen cold mills including a W 120 F, W 2000, three W 2100s and five new W 220s
Midstate's most recent mills are equipped with the Vacuum Cutting System (VCS), which reduces the amount of airborne material particles which are produced by cold milling.
"Without a doubt VCS is a real game changer," Johnson says. "We had the first in the state and now five of our newest mills have the vac system. And we had the first folding conveyors as well, they lower our liability when moving equipment."
Milling by Lake Superior
In July 2017 -- working as a subcontractor -- Midstate used one of its new 8-ft., 2-in. W 220 cold mills to remove aged asphalt from Wisconsin State Route 13 between Bayfield and Ashland, WI along the Lake Superior shoreline in the northern part of the state.
"We milled a total of 228,774 sq. yd. of S.R. 13," Mike Swing, project manager/estimator for Midstate says. "Our average milling depth was 3 inches. The existing pavement was about 25 years old and being somewhat brittle, it cut fairly easily as we were not going through a lot of teeth compared to other northern Minnesota and Wisconsin projects we've done."
The 10.7-mile project involved two 12-ft. driving lanes with 6-ft. shoulders on either side and approximately 38,000 tons of reclaimed asphalt pavement was produced with a top size of 2 in. That material will go to a plant location where it will be stockpiled and processed to a 0.75 to 1.0 in.-minus size for re-use.
"Typically on a day's run we would mill shoulders on both sides and then would mill the driving lanes afterward," Swing says. "Because we preserve the crown of the road, on each side of the centerline we would have 18 feet to cut and we would undertake three passes on each side of the center."
Wirtgen's Level Pro system on the W 220 kept the milling profile on target.
"The Level Pro is the top grade control system I've worked with," Swing adds. "We've never had a grade control issue when we've run Level Pro. It worked as it always has: very good."
On Wisconsin S.R. 13's driving lanes, Midstate was cutting 3 in. deep along the centerline and then carrying a 2.5 percent slope across the driving lane. The 6-ft.-wide shoulders were cut at a 4 percent slope.
Cameras at the end of the conveyor and at the rear of the machine for backup visibility, made views into the truck hopper and rear of the cold mill easily available from the operator's platform. The mill's VCS kept airborne dust and grit away from the workers and equipment while placing it on the conveyor and into the truck.
For this project, the Wirtgen WITOS FleetView system supplied Midstate an extraordinary information resource on day-to-day operations. FleetView keeps headquarters informed in real time of the location and operating state of every machine meaning that while the W 220 milled Wisconsin S.R. 13, it was linked to Midstate's home office 236 miles away.
"I really like the fact that using FleetView, I can see what each crew is doing on each project in real time," Swing says. "It tracks where each machine is at any time and provides production rates, equipment condition, everything. Even if they can't have cell phone service I can see where they are. And it's nice for our dispatch center as we can pinpoint where our equipment is."
The information also is archived for later use in case questions arise about the project or what transpired during milling.
Keeping Equipment Going
Midstate does not undertake paving projects by themselves, but uses its Vögele pavers and Hamm rollers to place and compact cold recycled mix from its in-place recycling trains. It has Hamm HD 130 HV, HD+ 140 VV HF (Tier III), and HD+ 140i VV tandem rollers. It uses two Hamm GRW 18 and one GRW 280i rubber tire rollers.
For soil compaction, it uses two Hamm H 11i rollers and a Hamm 3412. The double-drum HD+ 140i VV is outfitted with the Hamm HCQ Navigator system for intelligent compaction.
It has a new 10-ft. Vögele Super 2000-3i asphalt paver and two Vision 5200-2i pavers, like the rollers, used to place in-place recycled cold mix from its in-place recycle train.
And in addition to all this road work, Midstate continues its trucking activities with 30 "low boy" trailers in its fleet.
Keeping that durable roadbuilding equipment going throughout the season requires maintenance work during the off-season.
"During the winter months we run two rebuild shops," Johnson says. "We want every single piece of equipment to go through one of the two shops and expect it to come out 90 percent new following the rebuild. We hold ourselves to a very high standard on how well we maintain the equipment."
Operators are kept to a high standard as well.
"A lot of training goes on," Johnson says. "This equipment operates in a very abrasive environment. An inexperienced operator can destroy a drum in 10 minutes. Wirtgen equipment is very powerful, so we monitor the operators, starting with an intense training program."
Midstate works with two equipment distributors, Hayden-Murphy Equipment Co. in Minnesota and RDO Equipment Co. in North Dakota.
"While we do a lot of the equipment servicing ourselves, so much of fixing the problem is getting the supplies and parts," Johnson says. "That's why the incredible relationships that we have with our suppliers are so important. The support they give us is tremendous."
Midstate has been an active member of the Asphalt Recycling & Reclaiming Association (ARRA), and has worked within ARRA to promote these recycling methods throughout the country. Tom Johnson himself was ARRA president for 2006-07.
"Were it not for ARRA the trajectory of Midstate's curve would have been a lot different," Johnson said. "ARRA is a great platform for contractors like us and our relationship with ARRA is very symbiotic. We get help from them and they get help from us."
Tom Kuennen is a freelance writer in the surface transportation industry and can be reached at www.expresswaysonline.com.