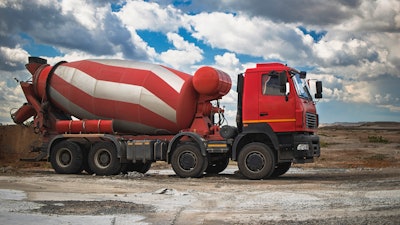
Everyone wants to be the first customer for the ready-mix truck. If all the material hasn’t been cleaned out, remnants of a previous mix can still be inside. It takes a good amount of water and a thorough cleaning to make sure the next delivery is one mix-design. Typically, it’s the ready-mix driver and supplier responsible for getting the drum ready for the next order.
In the event that it’s the contractor’s responsibility or you’re thinking about your own ready-mix plant, here are a few things to keep in mind.
The first question a concrete contractor will need to determine is if they are allowed to dump any excess on-site. Many construction sites will commonly have a pile of washed-up material somewhere off to the side of the site. Anecdotally, some contractors place the excess (not the washout) for a smaller project for the customer.
The washout, on the other hand, is ugly. But that’s why many prefer the truck to return to the ready-mix plant and run through their washout system there. This can clean out the drum better and, depending on the wash-out system utilized, the material washed may very well be reusable for jobs requiring lower-specification concrete.
At the Plant
At the ready-mix plant, designing an efficient washout system includes some key factors:
- Location — The right placement/layout in the yard equals speed for an efficient traffic pattern. The quicker trucks can get in, cleaned, and ready for the next delivery, the better. Consider the time taken for a truck driving 10 minutes to the end of a lot and back. How many lost minutes could that truck have been driving the next load of concrete? Also, ensure that trucks have enough space so they can safely drive in and out.
- Waste control — How is the system reclaiming material?
- Operation — Is the system easy to operate? Is the system easy to navigate?
- Cleanliness — Consider the mess. Balance the distance and time trucks must travel in the yard to the proximity to buildings.
When you think about it, optimizing the efficiency of the washout system at the plant should enable it to deliver more concrete and maximize the utilization of trucks in a day.
Often, plants direct runoff water from the plant to the washout system for reuse, again and again.
Elsewhere
These factors also apply when the project needs a space on-site. Timing is everything here, and efficiency is king.
“If contractors are going to put a washout station at a large jobsite … being able to washout is going to save time and make that more efficient,” says Shane Schmutzler, president of Jadair International Inc.
He adds that while the needs are the same, size is the difference here. Portable washout equipment will likely be much smaller than something more permanent at a ready-mix plant. The Jadair company manufactures concrete washout and clarification systems. The company was started by Schmutzler’s grandfather in 1969 with a system designed for use with wet air scrubbers, the Settler/Clarifier System, which was then redesigned for use in mining. Based in southeastern Wisconsin, they continue a 50-year legacy serving the mining, aggregate/sand/gravel, and ready-mix industries.
Consider the factors going into the planning of a good concrete washout space at the plant to the jobsite. There’s no time to spare — you must find that sweet spot of having it close enough to the site, out of the way, yet with easy enough access to allow the truck to get back into traffic.
A portable unit will need a source of water, and you will lose a little in the sand and gravel as the drum is washed out, but it’s not much. Past that, the majority of the water is self-contained and ready for the next truck (or job).
“If [contractors] are going to be moving from one site to the next,” adds Schmutzler, “the easiest thing would be to pump [the reclaimed water] into the container you brought to begin with.”
A Washed Concrete
There are two avenues contractors can look at regarding the “washed” concrete. One, is to use it right from the machine. Schmutzler explains that the sand and gravel are separated in their equipment, which is often used for lower-specification concrete projects. “Contractors will buy it outright because they like using it for base,” he says.
The other avenue is to use it as fill material. Washed-out material can be mixed with the virgin material, used as top cover for landfills, or mixed with sand for use on farms for the lime.
There may be discharge limits and environmental concerns that are specific to the area of construction. In the event that washing out the drum falls onto your shoulders of responsibility, it's recommended to know and understand what your state, city, and/or municipality codes and regulations are for the situation.