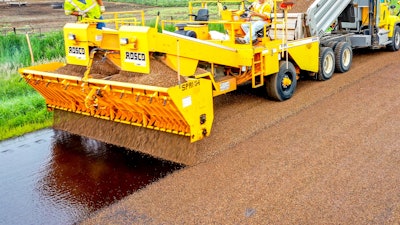
Mountaire Farms’ agricultural food production and processing facilities near Lumber Bridge, N.C., has its share of heavy, 18-wheeler traffic. The number of vehicles entering and exiting the facilities along with the location’s rainy climate has led to a higher degree of skid accidents when compared to other, similar locations.
When it came time for the North Carolina Department of Transportation (NCDOT) to revitalize the road surface, it was apparent the project needed to address this safety concern in addition to routine maintenance. NCDOT knew that these roads needed a high friction surface to help trucks and other vehicles slow and stop safely. However, calcined bauxite, the typical material used for high friction surface treatment (HFST) was cost-prohibitive.
NCDOT had a chip seal operation working nearby that was using expanded shale, clay and slate (ESCS) lightweight aggregate on secondary roads. This material had been used in other parts of North Carolina due to its high retention rate and ability to reduce the amount of emulsion necessary to reseal a road. It could also improve wet road traction. The Asphalt Surface Treatment Supervisor suggested to the Division Engineer that ESCS aggregate would be a viable alternative for a high friction surface treatment (HFST).
The justification is that ESCS has a network of internal pores that contribute to a higher surface friction that resists polish. The question is did it work? To understand the answer, it is first important to know the requirements around skid resistance and how ESCS works as a premium asphalt chip seal material.
What is skid resistance? Skid resistance measures the force that resists relative motion between a tire and the pavement. This measurement is dependent on both the macro- and microtexture of a pavement surface—both of which work together, especially in wet conditions.
The macrotexture of a pavement refers to the larger scale (0.5mm to 50mm) surface characteristics formed by individual aggregates or by grooves cut into the pavement. Macrotexture is the result of mixture design as well as methods of finishing. This aspect of pavement surfaces provides drainage channels for water to be expelled, allowing better contact between the tire and the pavement. Macrotexture is predominantly responsible for skid resistance at speeds over 56 miles per hour (mph). Microtexture, on the other hand, refers to the surface quality under 0.5mm. At this level, the paving surface and tire interact directly. This characteristic of a paving surface is largely dependent on the materials used and is responsible for skid resistance at lower speeds.
Macro- and microtextures come together to form a pavement’s overall skid resistance, which is often described in a three-zone diagram. Zone 1 refers to the space where a tire initially meets the pavement. The macrotexture allows fluid to drain and the tire to contact the pavement. Zone 2 is the space where the tire and pavement begin to fully connect—in this zone, a thin film drains through the microtexture of the paved surface. In zone 3, the tire has dry contact with the pavement. In this understanding, both textures are necessary for determining a pavement’s ability to provide adequate friction in wet or dry conditions.
DOT requirements for skid resistance
According to the U.S. Department of Transportation (USDOT), pavement friction, another name for skid resistance, is one of several factors that influences road safety. In the introduction to a 2023 primer of friction measurement and management methods, USDOT states that skid resistance is “explicitly considered in certain aspects of highway geometric design” and that pavement friction’s characteristics will vary over time, so it should be “managed throughout a pavement lifecycle, up until the very end-of-life.”
The Federal Highway Administration (FHWA) pavement policy within the Code of Federal Regulations indicates that pavements shall be designed to accommodate current and future predicted traffic needs in a safe, durable and cost-effective manner. Additionally, research conducted by the National Transportation Safety Board and FHWA indicates that about 70 percent of wet pavement crashes can be prevented or minimized by improved pavement friction. It follows then that skid resistance is an inherent component of pavement safety, so state departments of transportation (DOTs) often have their own recommendations for skid resistance based on the details of specific projects.
These recommendations also include monitoring pavements through a variety of tests and repairing them when pavement friction data dips below recommended values. The ability to maintain a consistently high level of skid resistance over time is one of the biggest challenges of designing safer pavements. Often, creating roads with long-term skid resistance comes down to the materials they are made of.
Polishing: how traffic reduces a material’s skid resistance
A pavement’s skid resistance can be reduced over a road’s lifecycle in several ways. However, polishing is perhaps the most seemingly inevitable. Polishing occurs as traffic, dust and debris smooth a pavement, specifically the aggregates that make up the road’s surface. While polishing most directly impacts the microtexture of a paving surface, it will also affect the peaks and valleys of the macrotexture to contribute to the overall reduction of a pavement’s skid resistance.
In locations with horizontal curves, steep grades, or intersection approaches (such as the ones at Mountaire Farms), there is a higher friction demand. This often leads to premature polishing. The reduction of pavement friction contributes to increased crash rates and less safe infrastructure in general. Because polishing is an evitable part of the wear and tear of a road’s surface, it is recommended that DOTs monitor its progression and take appropriate action when a pavement has been polished to the degree that it is no longer safe.
DOTs typically have two methods of combating polishing. The first is to resurface pavements on a regular basis, paying particular attention to locations that may experience premature polishing. The second is to use a HFST that resists polishing for longer than traditional limestone aggregates.
Lightweight aggregates: what are they and how do they work
Resurfacing pavements to mitigate polishing can be both cost-inefficient and inconvenient to constituents—especially in areas that commonly experience both heavy traffic and premature polishing. The other option can be equally expensive with some HFST materials. However, ESCS lightweight aggregate can provide a cost-effective high-friction pavement surface that also has a long-term resistance to polishing, due in part to its physical characteristics.
This material is produced by heating shale, clay and slate in a rotary kiln to temperatures around 2000 degrees Fahrenheit (F). During this process, air bubbles form within the expanding material. These air bubbles remain as a network of unconnected voids throughout the cooled aggregate. The material can then be crushed and sorted into highly regulated particle size. As such, ESCS can achieve a highly predictable amount of friction when compared to natural aggregates.
The voids within ESCS create a surface with a skid resistance that is significantly above limestone aggregate, approximately 65 for chip seal (compared to limestone’s 50) and 44 for hot mix (22 for limestone). Further, these lightweight aggregates do not readily polish as they wear. This creates a relatively stable amount of skid resistance over the pavement’s service life. While some degree of polishing is inevitable in application, ESCS lightweight aggregate resists polishing to extend the level of safety an asphalt can provide over its lifetime.
How this material contributes to longer lasting infrastructure
As stated above, ESCS lightweight aggregate resists polishing for longer than conventional aggregates. This, in turn, translates to asphalts that can provide an adequate amount of friction for safe driving for a longer period. Roads that stay safer longer not only reduce the amount of maintenance a DOT will need to plan for, but they also reduce the risk of liability DOTs may face if an accident occurs and the pavement’s skid resistance is deemed inadequate. Both aspects contribute to more cost-effective pavements, allowing DOTs to allocate resources elsewhere.
While ESCS can extend the safety a road provides by supporting long-term skid resistance, its network of voids also provides other benefits for longer lasting infrastructure. These voids increase the adhesion between the aggregate and the emulsion, which translates to less chipping and aggregate loss over the course of the pavement’s life. As a result, when used in asphalt chip seal, ESCS lightweight aggregates contribute to approximately a 40 percent longer service life than chip seals that use conventional aggregates. And in residential areas, the service life may extend up to 14 years.
Additionally, this material can provide retention rates of 99 percent, compared to the average 60 percent retention rate for natural aggregates, which contributes to a lower cost for resurfacing (as well as damage caused to vehicles from dislodged aggregates, due to the lower density of ESCS aggregates). Through the combination of immediate and long-term performance and resilience, ESCS lightweight aggregates can help roads stay safe and viable for longer. This not only decreases DOT spending in the long-term, but it also contributes to better road conditions for constituents.
Solve pavement challenges economically
The ability for ESCS to lengthen the amount of time a pavement is safe and useable is not just theoretical. It has been proven in several states, from Utah to Kansas, from Louisiana to North Carolina and more. Bolstering this data, the use of ESCS lightweight aggregates at Mountaire Farms contributed to a decrease in accident rates, demonstrating the material is an economical and practical alternative for HFST.
It is important to note that the long-term skid resistance numbers and retention rates of ESCS lightweight aggregate are not the only ways this material contributes to more economically efficient asphalt resurfacing. The NCDOT performed a return on investment (ROI) analysis on using ESCS. The results found that fine grade ESCS substantially increased the amount of area able to be covered by a similar amount of heavier aggregate while also using less oil. Further, the overall weight contributed to reduced transportation costs. Finally, its consistent quality gradation decreased blockages in spreaders for a more efficient use of labor. All of these reduced the overall cost of pavement maintenance while also contributing to a longer lasting and safer road surface.
Whether or not an asphalt pavement needs a high degree of skid resistance, asphalt chip seal that uses ESCS lightweight aggregate can be a cost-effective option and is worth consideration as DOTs look for ways to extend the service life of their pavements.