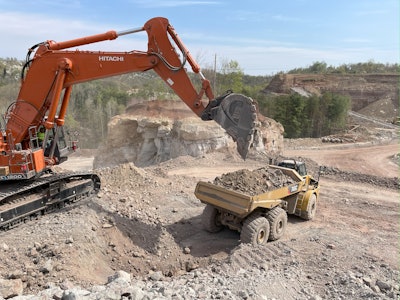
Tough jobs demand tough attachments. But just like no two job sites are the same, neither are two excavator buckets. Selecting the wrong attachment, per application, can become a costly mistake, from reduced performance to premature wear of the bucket and machine. The wrong attachment will affect your bottom line and return on investment. Machine downtime and additional labor can increase costs 10% to 20%.
With money and machinery at stake, let’s look at the factors that go into choosing the right bucket for your needs.
Selecting the wrong attachment, per application, can become a costly mistake, from reduced performance to premature wear of the bucket and machine.Werk-Brau
Material Abrasion & Impact
Material’s abrasion and impact factor into the type of bucket that best fits your needs. For instance, materials that are low on the abrasive scale with low impact such as topsoil, loam and coal are better handled with heavy-duty buckets. Medium abrasive materials with low to high impact such as sand, clay, gravel, shale, frost, travertine and limestone are application also well suited for heavy-duty buckets.
For higher abrasive materials with low to high impact such as high silica sand, caliche and shot granite, these applications are best suited for a severe-duty bucket. However, for projects with a steady diet of the most abrasive materials such as broken slag, sandstone, high quartzite granite and ore, extreme-duty buckets will be your best choice.
Heavy-duty buckets are recommended for trenching in utility work and are great for various construction situations.Werk-Brau
The Difference Between Heavy-Duty, Severe-Duty & Extreme-Duty Buckets
AR400 and T1(A514) steels are standard material grades you should ensure that are used in critical and high-wear areas in all excavator buckets. While heavy-duty buckets are one of the most popular excavator bucket styles, they are often chosen when application conditions vary or are not well known.
The design goes deeper than just the type of steel used. A flat bottom allows for easier load, unload, and backfill, while the dual taper/dual bottom plate radius allows for more efficient cleanout and fill. A high-strength top channel design prevents flexing and premature wear. Stacked bosses provide more durability than through bores which are commonly used on standard-duty buckets.
Selecting the correct bucket for a particular application will impact the project, bottom line and return on investment.Werk-Brau
Heavy-duty buckets are recommended for trenching in utility work and are great for various contractor situations. Designed with a thicker bottom and side wear plates for more durability, they also include pre-drilled holes for optional side cutters and shroud protectors. A wide range of tooth and shank assemblies are readily available for installation to make these buckets useful for many different use cases.
While severe-duty excavator buckets utilize AR400 and T1 steel like heavy-duty buckets, look for severe-duty lines that feature high-strength double-wear plates and heavy-duty wear straps, making them ideal for higher abrasive conditions. Their side wear plates are 40% thicker for added protection against abrasion and gouging wear.
These buckets are typically 20% heavier than heavy-duty versions but provide greater durability. The severe-duty cutting edge is thicker than its heavy-duty counterpart, and ground-engaging components are classed up to accommodate the application. This results in increased abrasion resistance. Severe-duty buckets have thickened cutter bits and are pre-drilled for optional bolt-on side cutters and shroud protection as well.
If there is a specific application, a specialized type of bucket may be best suited as opposed to a heavy-, severe- or extreme-duty bucket.Werk-Brau
Extreme-duty excavator buckets feature an aggressive dig angle, rugged construction of abrasion-resistant steel, and heavy-duty horizontal wear strips to efficiently excavate in the toughest conditions. Designed for durability and effectiveness even in brutal conditions, they are ideal for demolition work, shot rock, abrasive applications, moderate prying, and when paired with a thumb, material handling. The aggressive dig angle allows the bucket to tear through the earth and materials to scoop more efficiently. In addition, tapered side plates are engineered to reduce wear and allow for easier dumping.
Additional Excavator Bucket Types
If there is a specific application, a specialized type of bucket may be best suited as opposed to a heavy-, severe- or extreme-duty bucket. Ditching and grading buckets for instance are designed for cleaning ditches, sloping, grading and other light-duty finishing work. Their shallow depth and compact size make working in tight areas easy to empty and contain solids within the bucket. Heavy-penetration buckets, on the other hand, are used in heavy abrasive applications where breakout force and cycle times are important. In these buckets, the breakout force is maximized due to decreased tip radius and increased pin spread. Other common bucket types include:
- Scoop buckets — Designed to provide maximum digging performance
- Metro-style buckets — A combination of standard digging tooth and flared teeth, leave a smooth floor and minimal spillage
- High-capacity buckets — Designed for use in high production truck loading applications, move more materials in a minimal number of passes
Selecting the correct bucket for a particular application will impact the project, bottom line and return on investment. Nobody wants to buy more than is needed, but buying too little can be costly too.
When in doubt about which bucket or attachment is best for your application, ask your dealer sales rep or the bucket or attachment manufacturer for assistance.